As America experiences increased labor shortages and number of unfilled job positions, we can view it as an early warning to industries to explore cost savings options such as improving efficiency and reducing labor needs. But what can cost savings look like for the apparel and fashion printing industry? How do we navigate labor shortages from resign to hire? What can we do with our current staff to ensure they feel they are growing with a company and not against it? Let’s explore different avenues from why employees leave to attracting current talent and how the OvalJet might be able to assist in the long-term cost-saving goals of your organization.
You’re Leaving? Won’t You Stay? Why?
What is your first move when you receive the dreaded news that a top performing employee is leaving for a new opportunity? Review the job description, post the application online, maybe beg them to stay?
You can always approach the employee with a competitive raise, but what happens if they continue with the new opportunity? The departing employee’s job description has likely changed, and the employee might be your best person to assist with the update. They can create a standard operating procedure for their role, help update the job description and duties, and give the supervisors an idea on how to maintain the next employee in their exit interview.
A July 2021 poll conducted by Monster1 found that:
- 86% of workers feel that their career has stalled during the pandemic
- 29% of workers named lack of growth opportunities as their reason for wanting to quit
- 80% of workers do not think their current employer offers growth opportunities
- 49% of workers expect their employer to play a part in career development
Experts say that employees who believe their employers make effective use of their talents and abilities are overwhelmingly more committed to staying on the job. So how can we as an industry move forward with this information? Help our employees grow seems like the right answer, but the answer doesn’t always come with a clear path to the solution.
How is OvalJet helping their clients grow? Upon install of a new machine, many companies allot a certain amount of time training the future machine operators and that is it. When it comes to an OvalJet install, our technicians spend two weeks on an install and training, then an additional week of training future operators on their new machine. If there is an opportunity to cross train, the technicians welcome the opportunity. The OvalJet team trains from of a Standard Operating Procedure provided to the client that includes maintenance schedules and production guides.
“A FY22 goal for the OvalJet Service team is to develop new training options for our customers,” says Jerry Perez, 240 Tech LLC – OvalJet Service Manager. “We are developing options including high-quality on-demand video trainings to allow them to grow in their craft and train within the organization.”
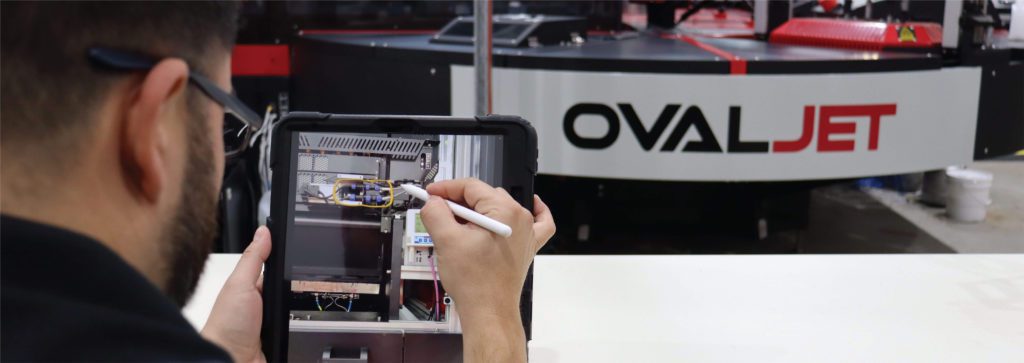
“With the launch of TeamViewer AR with our current customers we’re increasing up time. We’re able to resolve issues immediately utilizing augmented reality (AR) to troubleshoot and assist in real time, as opposed to our customers waiting for a technician to arrive at their facility for machine maintenance. We have exciting growth opportunities for our OvalJet operators coming to our portal this year.”
Providing staff with on-demand training allows for a flexible training schedule that ensures minimal disruption of business operations. Adding videos supports the standard written practices and assists with individuals with different learning styles. Consider your current employees your audience and ask them how they learn best to help prioritize learning materials.
Attracting Your New Talent
How do you source talent – LinkedIn, Indeed, recruiters? A job posting can often be the first thing a potential job candidate sees about your company, and if you can’t market your company in that moment, you may have lost that candidate forever.
When asking OvalJet internal staff, how the screen printing and DTG industry can attract new talent, Senior Technician, Dakota Sizemore recommended, “[We] target ambitious employees and give them resources to keep learning. Utilizing fresh brains will keep company moral up and further the drive within the technical and management teams.”
How do we attract those ambitious employees to OvalJet? Often, it’s word-of-mouth referrals from our internal team. Dakota really sells the company; we might add Dakota’s testimonial to all OvalJet job postings. We also give an engaging job description to all postings. We aren’t in the contract printing business we’re selling high-speed DTG printers to the contract printing business.
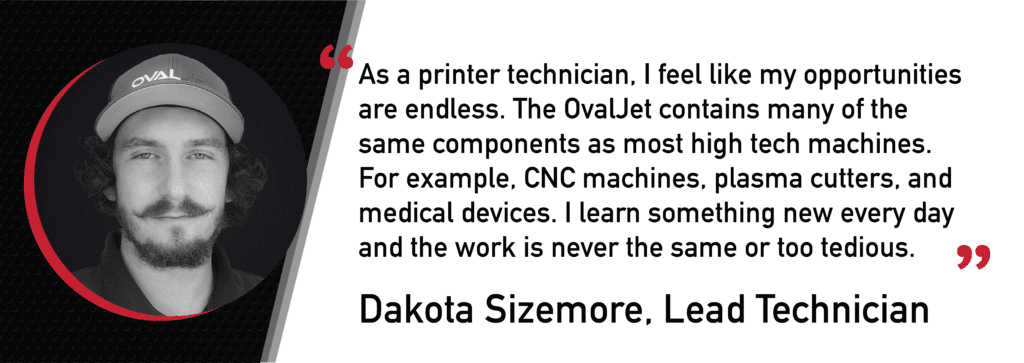
Get your job title right, are you hiring a Direct-To-Garment (DTG) Printer Operator or a Printer? Give a short and engaging summary of the position. As of February 2022, you’ll find many positions posted with minimal information on the machines the employees will be working on and little to no information on potential growth in the field.
The ideal job posting for your next rising star should give them an idea on:
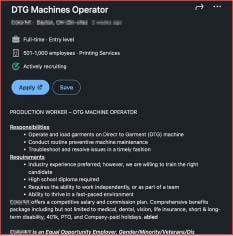
- The company’s culture,
- The required and optional qualifications (including equipment and software use/knowledge,
- Education requirements,
- Training opportunities (Are you willing to train someone on the machine with no garment printing experience? Are there opportunities to learn more than the current machines?),
- Work Schedule,
- Salary,
- Benefit Packages, and
- The standard EOE statement
And just like that, you have sparked interested in qualified candidates and dissuaded unqualified applicants.
Aligning Retention with Internal Mobility
Filling a position within an external candidate can be costly, with estimates of at least $3,079.2 So, can you explore hiring from within? Internal mobility is not a replacement to hiring new talent, as the promotion opens their previous role.
Or does it? We’ll come back to this in “Maybe It’s Time for a Change?”
The employee promoted is likely an expert on the open position and can assist in finding and training the best candidates to fill their former roles. Internal mobility can help staff feel more involved in the organization as a whole and lead to increased employee retention rates.
78 percent of employees say a clear career path would compel them to stay with an organization longer.3 What does a “clear career path” look like?
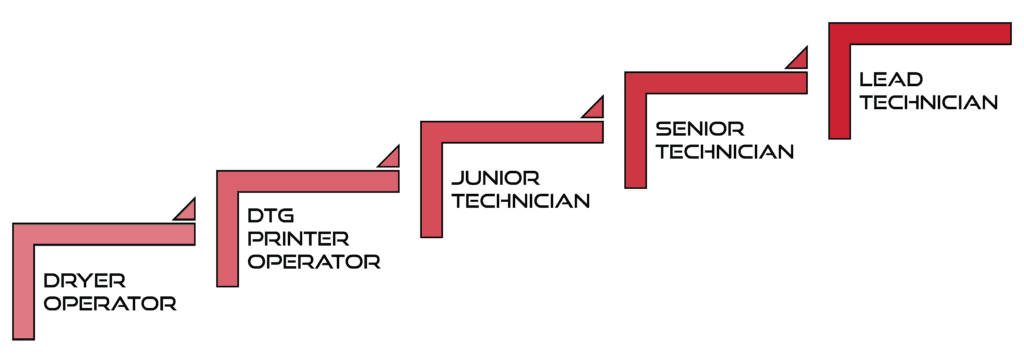
Well, a clear path varies by role in the organization and the employee’s drive. In Dakota’s case, he started as an inventory receiver. Then with his ambition, he trained to become an operator and technician in two years. As of July 2021, Dakota is the Lead Technician at 240 Tech LLC – OvalJet and we feel he can only grow from here.
Maybe It’s Time for a Change?
- Lower cost per labor – screen printers have a higher learning requirement and require more time per print (No need to prepare stencils or mix inks)
- Cost savings per print for multi-colored designs
- Unlimited color options, including gradations and transparencies
- Quick print turnaround, upload artwork and RIP (Raster Image Process) to a machine and print rather than screen setup
- Ability to accept short run prints, or one-offs
Links:
1 Monster, Monster Job Index
https://learnmore.monster.com/job-index-in-the-time-of-coronavirus
2 How Learning Programs Attract and Retain Top Talent : LinkedIn Learning
https://business.linkedin.com/content/dam/me/learning/en-us/pdfs/lil-guide-how-learning-attracts-retains-top-talent.pdf
3 Mercer, One in Three Employees Claim to Have a Job Rather Than a Career
https://www.businesswire.com/news/home/20150812005906/en/One-in-three-employees-claim-to-have-a-job-rather-than-a-career-new-Mercer-survey-finds
More To Explore
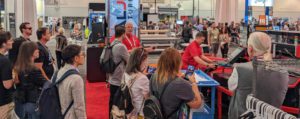
OvalJet at PRINTING United Expo
“Customers have told us, ‘If there was a Best In Show award, OvalJet would have received it,’” said Tom Grinstead COO of 240 Tech.
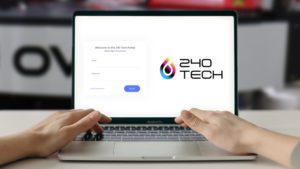
Service Ticketing Support on the 240 Tech Portal
This new system will allow us to service machines quicker, provide real-time status feedback and updates, and give us a long-term record of any reported issues. These records will help us to continuously improve the OvalJet and the overall user/technician experience.